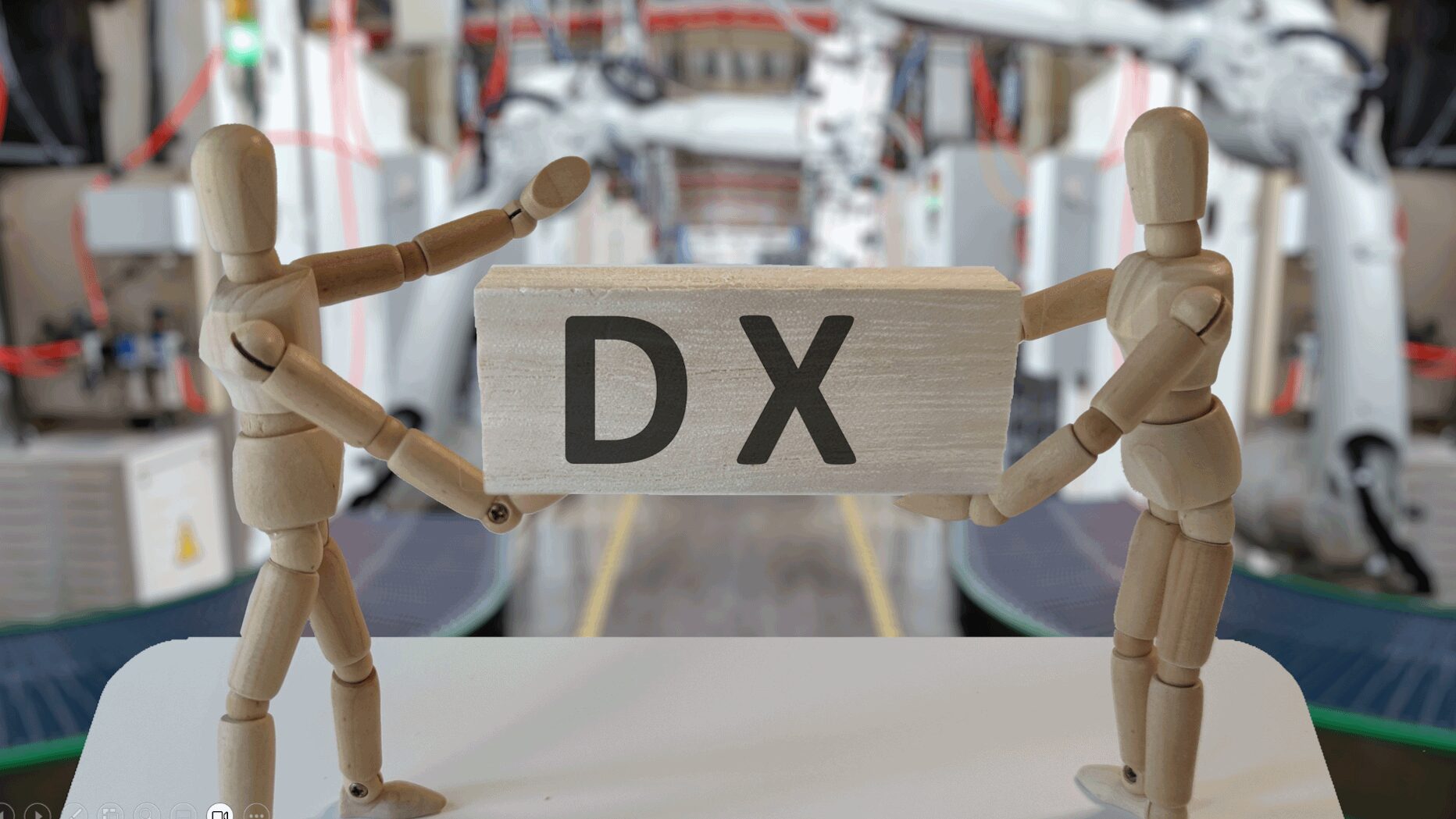
製造業におけるデジタル化の波は、年々その勢いを増しています。
中でも注目されているのが、工場のIoT化・自動化を推進するスマートファクトリー。
生産性向上や品質改善、働き方改革など、多くのメリットが期待される一方で、既存設備との連携やデータの活用といった技術的なハードルも存在します。
今回は、そんなスマートファクトリー化を目指す大手製造業様を支援した、当社のITシステム開発の取り組みをご紹介します。
お客様が抱えていた課題
本プロジェクトのエンドユーザーである大手製造業のお客様は、スマートファクトリーの実現を目指しておられました。しかし、現状の生産ラインでは以下のような課題を抱えていました。
設備ごとの制御がバラバラで、省人化が進まない
製造ラインには各種メーカー製の設備が導入されており、それぞれが独立したPLC(プログラマブルロジックコントローラー)によって制御されていました。
そのため、オペレーターは設備ごとに制御盤まで出向いて操作・確認を行う必要があり、多くの人手がかかっていました。
パラメータ設定が属人化し、品質管理にばらつき
製品品質を維持するためには、各設備で天候などを加味した適切な設定値(パラメータ)の調整が必要ですが、それらのノウハウがベテラン社員に属人化(職人化)しており、暗黙知となっていることが品質リスクにもなっていました。
設備の状態が見えず、予防保全ができない
現場ではトラブルや停止が発生してから対応する事後保全型のメンテナンスが主流で、設備の故障予兆を事前に捉えることが困難でした。
これにより突発的なライン停止や品質トラブルのリスクが存在していました。
解決アプローチ|PLC統合+ITシステムで一元化と可視化を実現
こうした課題を解決するため、私たちは元請け企業(PLC・設備工事事業者)と連携しながら、以下のようなアーキテクチャを提案・構築しました。
異種PLCの統合と一元管理
各設備が持つメーカー独自の既存PLCを、統合するPLCを新規設置することで一元的に管理する仕組みを導入しました。
これにより、現場のオペレーターが設備ごとに移動する必要がなくなり、省人化が進みました。
ITシステムによるデータ蓄積・可視化・遠隔操作
PLC単体では実現が難しい、データの蓄積やタブレットなどによるリモート監視・操作機能を実現するため、統合PLCと連携するITシステムを新たに構築。
このITシステムにより、以下のことが可能になりました。
- 各設備の稼働状況やエラー情報のリアルタイム表示
- 履歴データの蓄積と分析による予兆検知
- タブレット端末からの遠隔制御・監視
- パラメータの一元管理による品質の標準化
このように、「現場の見える化」と「リモート化」を実現する基盤を整えました。
実現できたこと・得られたメリット
この取り組みにより、製造現場に以下のような改善と価値をもたらすことができました。
- オペレーターの省人化:現場を巡回せずに複数設備をリモートで操作可能に
- 運転管理の一元化:統合PLCとITシステムにより、すべての設備状態を集中管理
- 品質の安定化:設定パラメータの標準化・可視化で属人性を排除
- 稼働状況の見える化:異常・停止・エラー情報をリアルタイムに把握
- 予防保全の実現:履歴データをもとに傾向分析し、故障の兆候を事前に察知
- DXの第一歩を実現:スマートファクトリーに向けたデジタル基盤を構築
今回のシステム構成
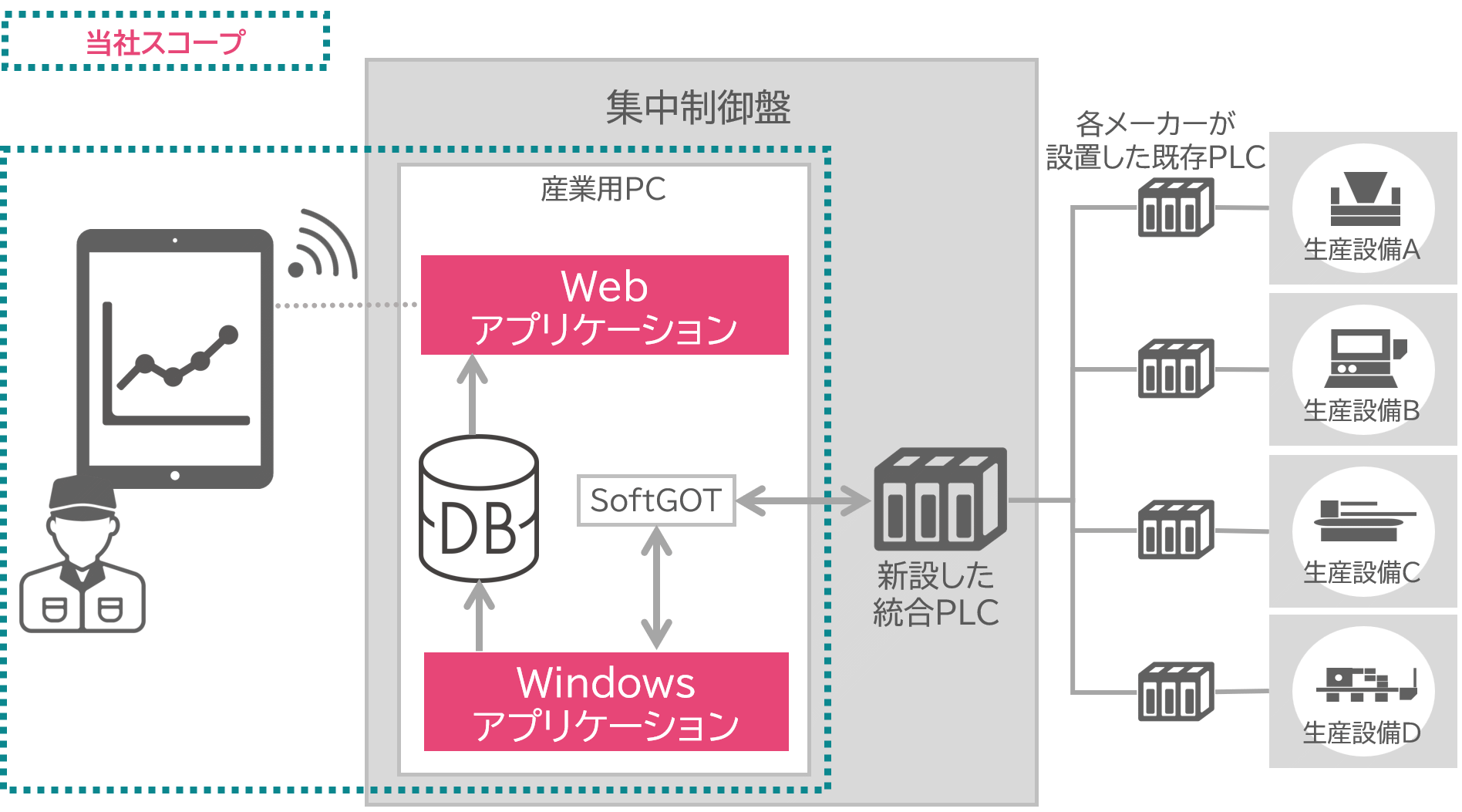
技術要素:ASP.NET(C#)/IIS/JavaScript/SQL Server/Windowsアプリケーション(C#)/Soft GOT
※iPadからはブラウザ経由で利用
さいごに|現場を理解し、伴走するシステム開発パートナーとして
本プロジェクトでは、設備やネットワーク敷設工事なども含めた大規模な構想のもと、当社は元請け企業様と密に連携しながら、ITシステム部分を担当しました。
ただ「システムを作る」のではなく、製造現場の業務や課題を深く理解したうえで、最適な解決策をご提案・実装することを心がけました。
私たちは、今後も「技術だけでなく現場を理解するシステム開発会社」として、製造業のお客様のスマートファクトリー化、DX推進を支援していきたいと思います。
システム開発 無料お悩み相談 このようなお悩みはございませんか? システム開発について良く分からず、何をどう相談したらよいか分からない、システムを発注したことがない ハードウェアがいつ故障してもおかしくないがシステムを新 …